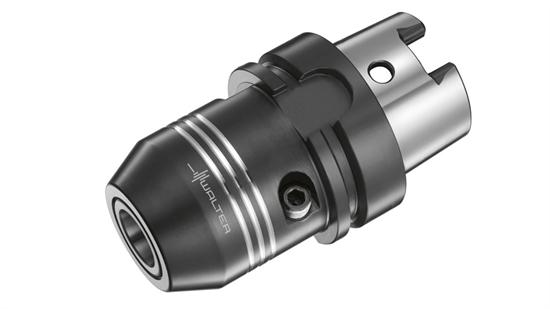
Previously, the hydraulic expansion clamping principle has been predominantly a toolholding technology for drilling, and, in milling operations, it was mainly used for finishing. With the AK 182, Walter is now launching a hydraulic expansion chuck onto the market which, due it is high degree of concentricity and damping, is also suitable for roughing.
The new Walter hydraulic expansion chuck meets all the requirements of a modern, powerful and high-precision chuck. The design features vibration-damping properties which significantly reduce the risk of the tool coming loose due to vibration, particularly during milling. It also has a positive effect on tool life. Compared to the hydraulic expansion chucks and collet adaptors produced by Walter's competitors, it is possible to transmit significantly higher torques: this means the tools can therefore also be used for roughing. In addition to roughing and finishing as part of the milling process, the AK 182 is also suitable for drilling, reaming and threading.
The chuck's torque transmission of up to 900 Nm at a diameter of 20 mm, long-lasting concentricity and position repeatability of less than 3 μ (measured at 2.5 x Dc projection length) and the vibration-damping effect make particularly high cutting speeds and feeds per tooth possible. The chuck is particularly suitable for roughing with Walter Prototyp solid carbide milling cutters and also for thread milling. The AK 182 is the best clamping technology available for achieving outstanding machining results when drilling and reaming with Walter Titex tools.
The chuck is available for the popular SK40/50, BT40/50 and HSK63/100 machine interfaces and in three adaption diameters of 12, 20 and 30 mm. Smaller tool diameters from 3 to 25 mm can be clamped using reduction sleeves. There are no limitations on shank types. All tools with cylindrical shanks, and those which comply with DIN 1835 form B, E and DIN 6535 form
HB, HE, may be clamped without running the risk of destroying the chuck. The chuck will not be damaged even if you accidentally tighten it when there is nothing in it.
The reduction sleeves are available as a sealed variant or as a sleeve with peripheral cooling. This means that tools either with or without an internal coolant supply can be used. The sealed sleeve, just like the chuck itself, is designed for pressures of up to 80 bar. It is ideal for tools with an internal coolant supply, of the kind that are increasingly required these days for drilling, as well as for milling and reaming. The coolant in the sleeve designed for external or peripheral cooling is transported forwards via slots over the shank, and from there it is conveyed via an ingeniously designed profile channel into the tool flutes and down to the cutting edge. This solution is particularly advantageous for milling cutters without coolant channels, since this is an excellent way to convey the coolant to the cutting edge.
The length of the tools can be set precisely, and the tools can be clamped against an adjustable stop. This enables the chuck to cover a wide spectrum of tool diameters. In comparison with shrink-fit adaptors, which have a different adaptor for each diameter, savings can be made with the tool change and adaptor sleeve system.
The chuck's vibration damping increases tool life by up to 40 percent. Handling it couldn't be easier. The chuck can be tightened or released using a conventional hexagon key. The AK 182 has been available since April. Laboratory tests demonstrate that it is one of the best hydraulic expansion chucks on the market. |